As the world continues to grapple with the Covid-19 pandemic for the past two years, we remain committed in our efforts to develop, engage and retain talent despite the challenges arising from the pandemic. We reinforced our culture of adaptability by moving quickly to identify new ways of working and ensuring that there is dynamic business continuity throughout the Group to support our continuing growth and success.
HEALTH AND WELL-BEING INITIATIVES
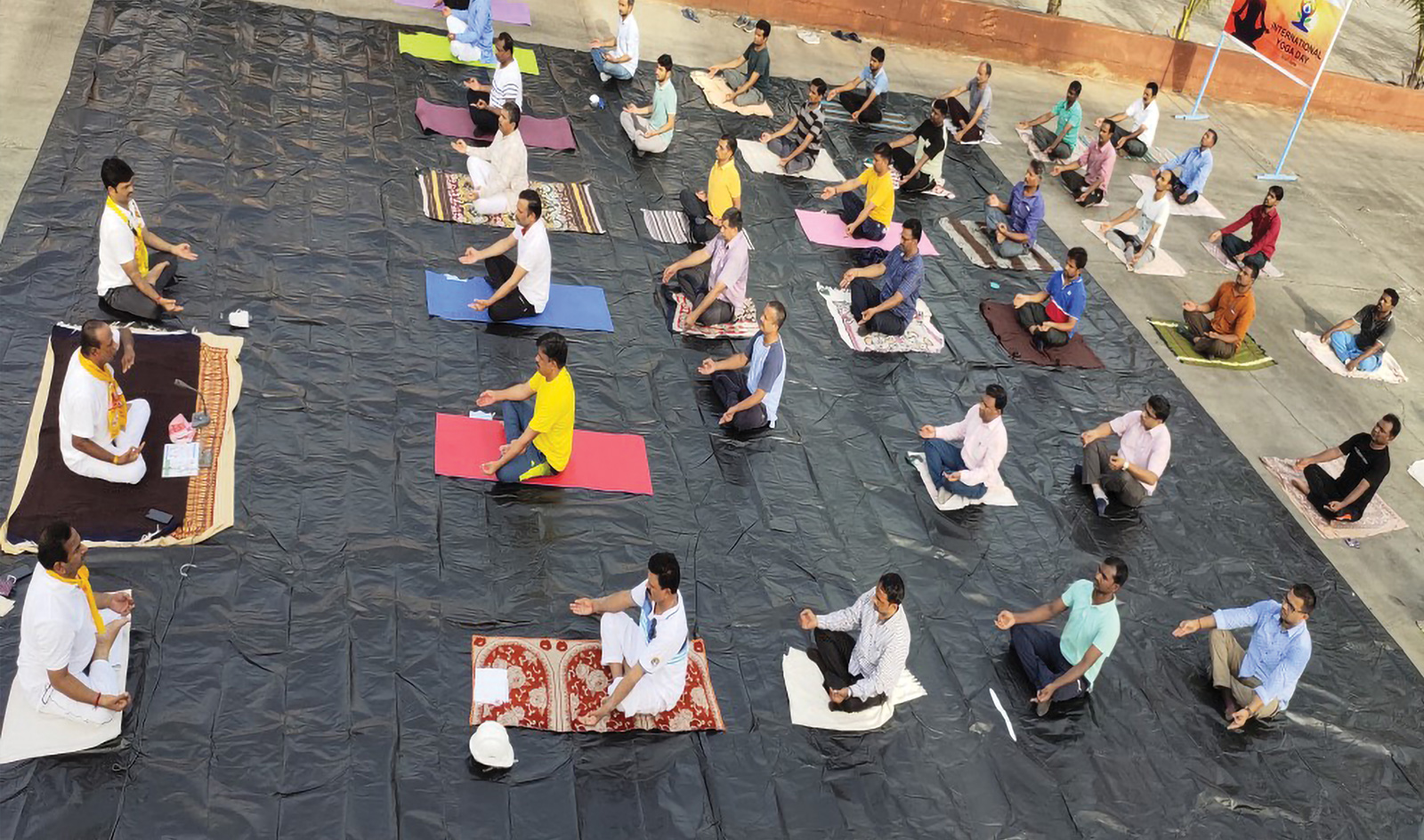
The pandemic has underscored the importance of good health in fighting the virus and we endeavour to ramp up more health and well-being initiatives amongst our employees.
In 2021, we kickstarted numerous wellness programmes and initiatives globally to promote a healthy lifestyle. These included yoga classes and virtual seminars and workshops on topics such as mental health awareness and ergonomics.
To establish a strong support system for mental health, 40 employees from Goodman Fielder, our subsidiary in Australia, received training and are now certified Mental Health First Aiders (MHFA) who are capable of managing a mental health crisis should it happen at the workplace. Throughout September 2021, Goodman Fielder also launched “Thrive Together” – a month-long programme where over 20 different virtual activities were held for the purpose of improving emotional, social and physical well-being amongst employees. 83% of employees indicated in post programme surveys that they have benefited much from the programme.
INVESTING IN THE GROWTH OF OUR WORKFORCE
Wilmar seeks to attract hardworking, agile and innovative individuals who create value and thrive in our fast-paced business environment. We collaborate frequently with the local technical institutes and universities to extend career opportunities such as apprenticeships and internships to their students.
INNOVATION
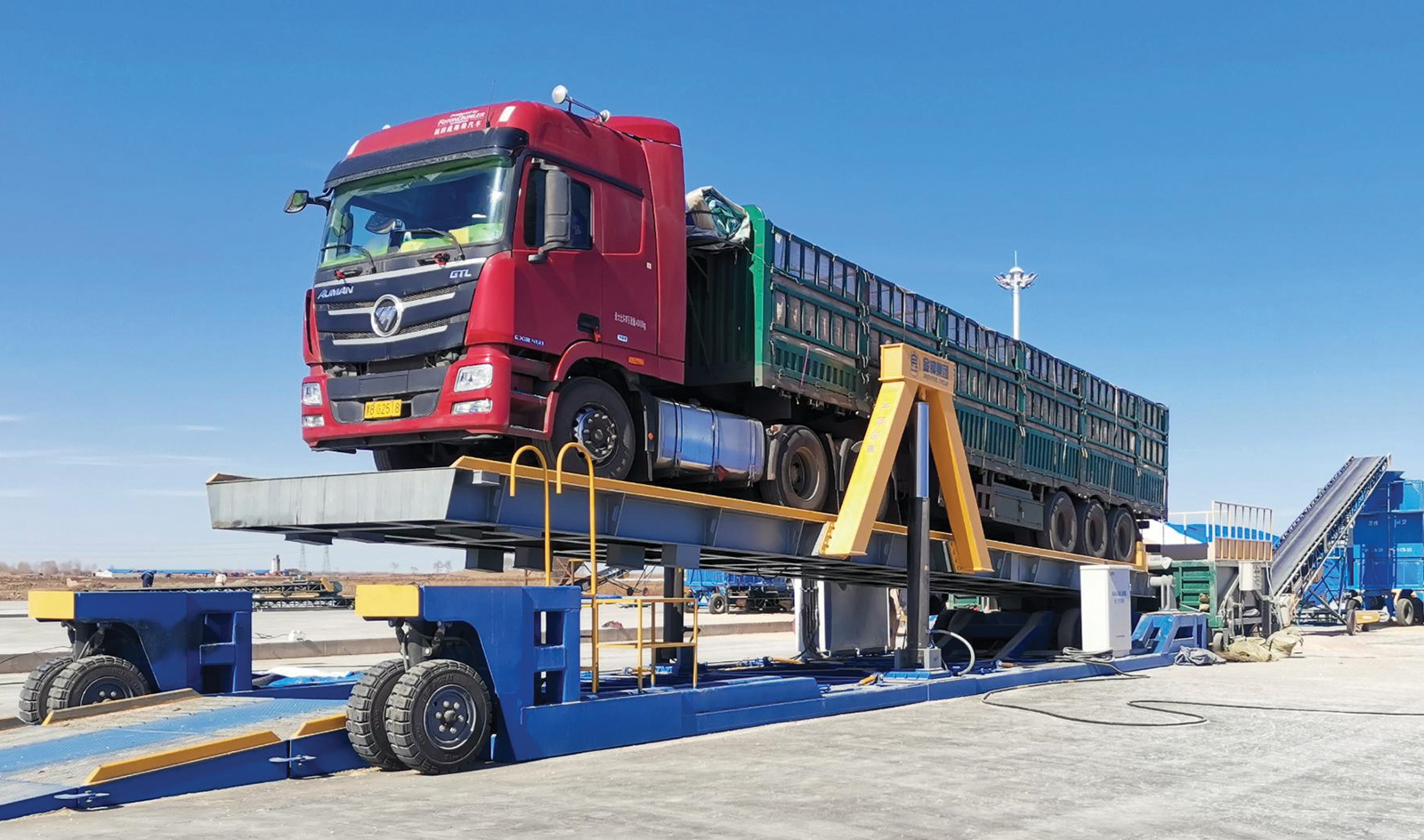
Innovation is one of Wilmar’s core values and is strongly encouraged across all business units. It is a key driver of business growth and gives us a competitive edge which is particularly critical amid an uncertain business environment.
Our team in China constantly ideate and implement tools to optimise our supply chain and enhance its efficiency. For instance, to increase the accuracy for our packaging production line in our Bazhou factory, we reformed a few processes, added new automation tools and made adjustments to the manipulator programme. The reduction of manpower usage as well as wastage from packing scale inaccuracy have resulted in a monthly cost saving of RMB 20,000.
With the number of onsite employees being restricted by the pandemic, we took the opportunity to automate our materials unloading system with a remote-controlled hydraulic turning machine in suitable facilities across China. This replaces the conventional process where workers are required to manually open the unloading door of the truck and subsequently utilise an equipment to conduct a retrieval. The automation enhancement has reduced operational costs by RMB 2.55/tonne and improved the safety aspect of our operations.
In October 2021, Goodman Fielder completed its first electric vehicle trial, using a JAC N55 truck in Queensland. The learnings from the trial allowed Goodman Fielder to understand the usage of electric vehicle technology and how it can play a bigger role in logistics and supply chain. These insights contributed significantly to Goodman Fielder’s goal of achieving net zero carbon emissions by 2040 to support and embrace a more sustainable and pollution-free environment.
Wilmar will continue to create a safe and healthy working environment for our employees amid the pandemic, while strengthening our Human Resource strategy to enable every employee to reach his fullest potential.